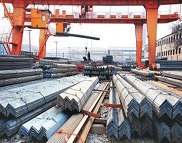
China underwent rapid economic industrialisation since Deng Xiaoping's capitalist reforms which took place 3 decades ago in 1978.
The steel industry gradually increased it output. China's annual crude steel output was 100 million tons in 1996.
It produced 123 million tons of steel in 1999. After its ascension to the WTO it aggressively expanded its production for its growing appetite of manufacturing industries such as automotive vehicles, consumer electronics and building materials.
The Chinese steel industry is dominated by a number of large state-owned groups which are owned via shareholdings by local authorities, provincial governments and even the central authorities. The biggest steel groups are Baosteel, Angang Steel Company, Wuhan Iron and Steel, Anshan, Tangshan, Shagang Group and Hebei Iron and Steel.
In 2008 raw materials such as Iron ore prices grew and China had to reluctantly agree to price increases by the three largest iron ore producers in the world; BHP Billiton, Rio Tinto and Vale.
During the Global financial crisis the Chinese steel mills won price reprieves as demand from their customers slowed. When the demand started to pick up again in 2009 and in 2010, the price crept back up due to higher demand for automobiles, low interest rates, government fiscal stimuli around the world.[6] Prices for iron ore were negotiated on an annual contract pricing scheme.
Australian iron ore producers were not happy that iron prices did not reflect Spot market pricing. In 2010 pressure from BHP Billiton and Rio Tinto to move to a quarterly based index pricing succeeded.Many Japanese steel mills and Chinese steel companies had to follow as demand for raw materials heated up.
Spot-basis pricing has caused problems for steel manufacturers such as exposing them to price fluctuation in the market and reducing the stability of resource supply. Steel mills prefer long term pricing to hedge against cost and maintain raw material supply stability.
Rio Tinto has said it will cancel contracts and sell the steel on the spot markets if Chinese steel mills back down on the new quarterly pricing regime.
In 2011 China was the largest producer of steel in the world producing 45% of the world's steel, 683 million tons, an increase of 9% from 2010. 6 of 10 of largest steel producers in the world are in China. Profits are low despite continued high demand due to high debt and overproduction of high end products produced with the equipment financed by the high debt. The central government is aware of this problem but there is no easy way to resolve it as local governments strongly support local steel production. Meanwhile, each firm aggressively increases production.[15] Iron ore production kept pace with steel production in the early 1990s but was soon outpaced by imported iron ore and other metals in the early 2000s. Steel production, an estimated 140 million tons in 2000 increased to 419 million tons in 2006. Much of the country's steel output comes from a large number of small-scale producing centers, one of the largest being Anshan in Liaoning.
China was the top exporter of steel in the world in 2008. Export volumes in 2008 were 59.23 million tons, a 5.5% fall over the previous year.[16] The decline ended China's decade-old steel export growth. As of 2012 steel exports faced widespread anti-dumping taxes and had not returned to pre-2008 levels. Domestic demand remained strong, particularly in the developing west where steel production in Xinjiang was expanding.
On 26 April 2012 a warning was issued by China's bank regulator to use caution with respect to lending money to steel companies who, as profits from the manufacture and sale of steel have fallen, have sometimes used borrowed money for speculative purposes. According to the China Iron and Steel Association the Chinese steel industry lost 1 billion Rmb in the first quarter of 2012, its first loss since 2000.
Guangdong Shunde Seko Machinery & Technology Co.,Ltd.www.gdseko.com
Lucy Xie
sevvice@gdseko.com
Skype:Lucy Xie,SEKO Machinery
Suggested Reading:Knowledge of the steel